Manufacturing Chemist Magazine
High purity water innovation wins Cleanroom Technology award
This month's Manufacturing Chemist Magazine features an insightful article honing in on the recent award successes at Honeyman Group. Transcript of article below, with link to live article at Manufacuring Chemist Magazine.
Honeyman Group continues to build on its patented system for bulk pure water distribution, HydroGienic® , which has been showered with accolades
For sectors such as the pharmaceutical and biotechnology industry, high purity water is vital to manufacturing facilities. HydroGienic®, a bulk pure water distribution system developed by Honeyman Group, has been designed to address the problems and restrictions associated with existing systems in these markets.
At the recent Cleanroom Technology Conference, held in May 2018, its inaugural awards saw Honeyman receive the Best Innovation Award for this pharmaceutical water distribution system. The company also recently received a Queen’s Award for Innovation for the same product.
The judges of the Cleanroom Technology awards stated that: “This game-changing innovation not only provides economic advantages and ease of installation, it also offers flexibility, sustainability and overall operational benefits.”
Tom Honeyman, Managing Director, said: “We are delighted to have won this highly specialist award from an area at the epicentre of our industry and into which we deliver critical utilities and services — the cleanroom.”
Typical water distribution networks work on a mains style stainless steel ring layout. This means that if one part of the facility requires changes to its water supply, the whole system has to be closed down and revalidated before it can be used again.
This can lead to disruption in production, which can result in significant costs.
The HydroGienic® system utilises a central storage tank, with each area of the factory supplied through its own send and return PTFE hoses. These are connected through a specially designed plug and play chamber. User points can be added or moved without disrupting existing production. It is suitable for all grades of water, including pure water and water-for-injection (WFI), in hot and cold loops.
If an issue is detected, by working on only parts of the network, the HydroGienic® system enables production to be maintained while any problems are isolated. It also reduces spending on externally sourced water. When a network needs to be expanded, increasing the number of distribution points can also be done with minimal impact on production.
HydroGienic® offers a guaranteed flow rate irrespective of time of day or usage in other areas. Plus, phased installation is possible to provide a fully validated water system prior to commissioning. Furthermore, individual user points can be added or moved without disrupting the water supply to any existing ones, which reduces downtime and saves cost.
Problematic or inefficient pure water systems have a detrimental impact on production sites, which is why an innovation such as HydroGienic® offers a practical solution to the pharmaceutical and life sciences sectors. Introducing new and disruptive technology in a profoundly regulated market such as the pharmaceutical industry is very challenging.
Organisations are often reluctant to be early adopters, despite clear advantages. However, according to Honeyman, HydroGienic® is rapidly gaining trust and popularity.
Honeyman said: “The HydroGienic® system is tried, tested and trusted; it’s a pure water distribution system for forward thinking pharmaceutical manufacturers.” The next steps for the development of the HydroGienic® system are with the associated water purification system, PureGienic. The company is investing in increasing its manufacturing space and capabilities for the PureGienic pretreatment and purification system. PureGienic produces 200–20,000 L/h. HydroGienic® can then store and distribute this water to as many offtakes as required within a facility, at a specified flowrate, regardless of system usage. Where facilities need to have modular flexibility and be adaptable to meet their changing production requirements, Honeyman believes that project installation timescales and cost will be enormously reduced with this technology.
See magazine article in full here, manufacturing chemist June 2018.
To Request Further Information Please Contact Us:
Contact UsOur Customers:
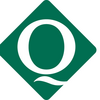
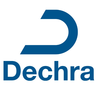
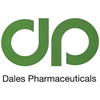
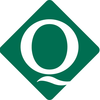
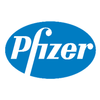
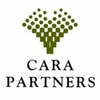
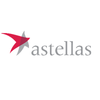
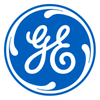
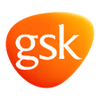
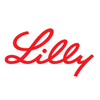
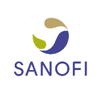
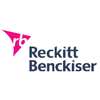
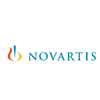