Routine & Call-out Maintenance
Solving intricate Purified Water & WFI challenges
Routine and Call-out Maintenance
Our experienced field service team provides routine service and maintenance on
- Pre-treatment,
- RO / EDI PW systems,
- WFI generation systems,
- Storage and distribution systems,
- Rapid breakdown and emergency call-out support
- Chemical cleans of RO systems and EDI’s.
In addition to our own PW generation skids and installations, we maintain a wide range of different manufacture’s skids.
From incoming towns water to every point of use and anything in between, Honeyman Water can ensure its reliably serviced and maintained. We can conduct preventative and reactive maintenance including; resin changes, RO membrane replacement, chemical cleans and diaphragm replacements. Our experienced site engineers are passionate about your system and will go to great length to minimise disruption to your site and can attend site a time most suitable to you including out-of-hours, evenings, night shifts or weekends and Bank Holidays.
All service and call-out visits are subject to RAMS and come with a detailed electronic service report.
It is an expectation for all manufacturers within the pharmaceutical industry to ensure purified water systems are maintained to relevant pharmacopoeial (USP or EP/PhEur) standards, as laid down in the User Requirement Specification (URS) and as stated in the ISPE Baseline Pharmaceutical Engineering Guide®.
Each individual water/steam system should have a scheduled maintenance plan carried out at periods stipulated in the plan i.e. Weekly, Monthly, Yearly. It might also happen that unforeseen faults arise that need urgent attention. Don’t worry, at Honeyman we have you covered.
Our Services Include:
Urgent Call-out Response
Depending on your location within UK and Ireland, Honeyman Water can offer an 24-48h call out service to analyse or rectify your problem. Our engineers can also often support remotely, therefore, in any emergency, please contact Honeyman Water on +44(0) 1833 - 690101
System Health Checks
A full system health check to identify any risk of deficiencies or future flaws before non-compliance is reached. Our principal consultants will review your pure water/steam system and provide an overview and report on performance, compliance and management issues, bench-marked against current industry best practice and GMP.
Maintenance Schedule Plans
Reviewing, producing or updating a maintenance schedule plan. Honeyman will review your water/steam system's maintenance schedule plan and advice on actions that are needed to ensure your system maintains "good health".
Routine Maintenance
Carrying out routine maintenance as defined in the maintenance schedule plan. Our support team will carry out routine maintenance of your system. As part of this maintenance Honeyman will check all parts and material for wear and tear and replace where applicable.
Problem Diagnosis
If your water system develops any problems, Honeyman will advise on the best possible solution for your business, utilising our extensive knowledge of water/steam systems.
System Upgrades
Honeyman can upgrade your water/steam system to current industry standards to give you the best operational use and control of your system. Water Committee Representative
Backed-up by decades of experience in pharmaceutical water and steam systems, the Honeyman Group offer a range of solutions tailored to work for you.
We can take full responsibility for the maintenance of your pharmaceutical water/steam system. Honeyman can, in an efficient and effective manner, identify potential financial and operational risks that the current system might pose, allowing for rectification before any breakdowns arise.
To discuss how Honeyman can maintain your water or pure steam system, please contact us with your details and a brief introduction, so we can arrange a call back at a time convenient to you.
To Request Further Information Please Contact Us:
Contact UsOur Customers:
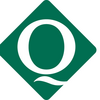
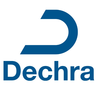
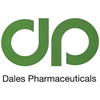
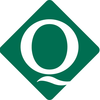
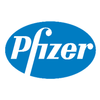
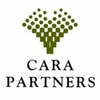
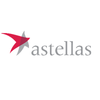
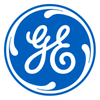
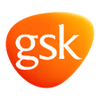
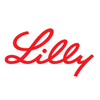
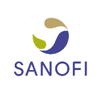
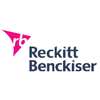
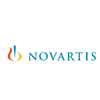